Georgia Tech’s GaMEP is Driving Innovation Across Georgia
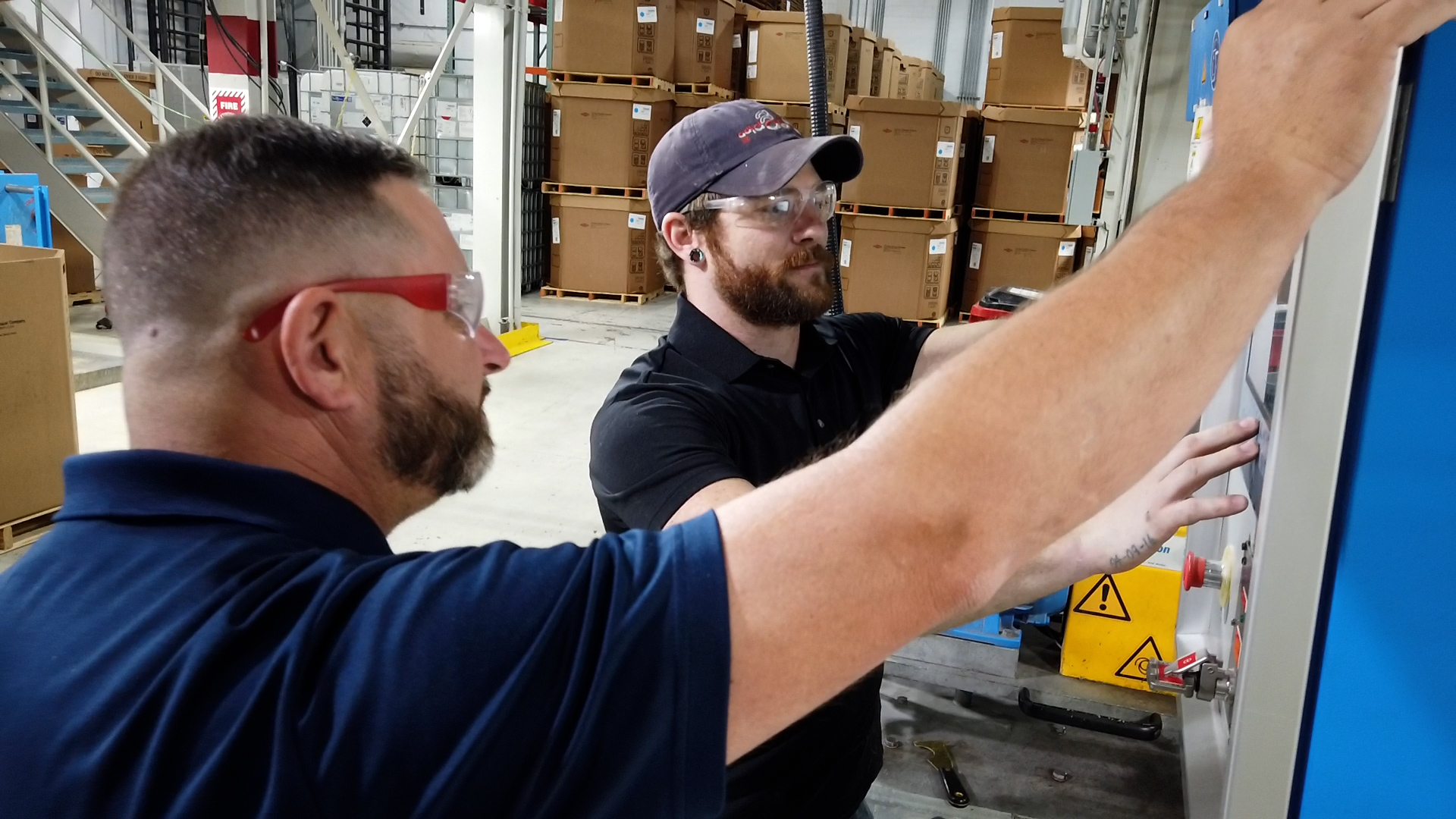
Lead technician, Austin Hicks, taps on a monitoring screen while his co-worker looks on at the manufacturing facility for Silon in Peachtree City, Georgia
“A stitch in time saves nine,” goes the old saying. For a company in Georgia, that adage became very real when damage to a key piece of machinery threatened its operation. The group helping with the stitch in time was the Georgia Manufacturing Extension Partnership (GaMEP), a program of Georgia Tech's Enterprise Innovation Institute that — for more than 60 years — has been helping small- to medium-sized manufacturers in Georgia stay competitive and grow, boosting economic development across the state.
Silon US, a Peachtree City manufacturer that designs and produces engineered compounds used to create a wide range of products — from automotive applications to building materials, such as PEX piping and wire and cable, was experiencing problems with their extrusion line during a time of increasing customer demand. Problems with the drive mechanism on that extrusion line, a piece of equipment critical to the company’s ability to produce, threatened to shut them down. With replacement parts several weeks away, was it safe to continue operating? At what throughput rates? How much collateral damage might be incurred if they continued to operate?
That’s when Silon managers turned to GaMEP for help.
After working through ideas with GaMEP’s manufacturing experts, the team installed wireless condition monitoring sensors that provide continuous, real-time insights on their manufacturing assets’ health. With the sensors, Silon was able to find a sweet spot that not only allowed them to continue operating but also kept them from overexerting the equipment, preventing further damage.
The solution to that problem has now become a routine part of Silon’s process, as company technicians continue to use this sensor technology for early detection of any deviations or anomalies in the machinery’s health, allowing the company’s maintenance team to proactively respond by adjusting scheduled maintenance to avoid costly downtime.
GaMEP’s Sean Madhavaraman says, “Silon is more productive than ever and on track for growth. The strong results in this challenge are a great example of the decades-long focus of GaMEP to educate and train managers and employees in best practices, to develop and implement the latest technology, and to work together with businesses to find solutions.”
Daniel Raubenheimer and Matt Gammon, Silon’s general managers, also lauded GaMEP, saying, “GaMEP’s extensive experience within the manufacturing realm has been a great benefit to our company. The wireless condition monitoring sensors allow us to predict future breakdowns and mitigate a potential catastrophe — allowing us to operate in a safe manner, while saving money, time, and effort.”